CHAPTER 1
INTRODUCTION TO CONTROL SYSTEM
1.1.1 Names the common application in electrical, pneumatic and hydraulic control.
1.2 Identify general terms used in process control.
1.2.1 Define process variables, dynamic variables, servo control, feedback control, process, regulation, set point, interference and error, controller, measurement elements and so on.
1.2.1 Define process variables, dynamic variables, servo control, feedback control, process, regulation, set point, interference and error, controller, measurement elements and so on.
1.3 Identify basic process control system:
1.3.1 Recognize the basic elements for process control (example level control in tank, temperature control etc).
1.3.2 Explain the process of measurement, evaluation and control elements from 1.3.1.
1.3.3 Draw and label block diagram of basic elements of process control.
1.3.4 Explain the purpose and use of open loop and closed loop block diagrams.
1.3.5 Differentiate open loop from closed loop process control by identifying negative and positive feedback.
1.3.6 Build examples of open loop and closed loop process control with the aid of block diagrams.
1.3.7 Define automatic control system.
1.3.8 Explain the purpose, advantages and disadvantages of automatic control system usage.
1.3.1 Recognize the basic elements for process control (example level control in tank, temperature control etc).
1.3.2 Explain the process of measurement, evaluation and control elements from 1.3.1.
1.3.3 Draw and label block diagram of basic elements of process control.
1.3.4 Explain the purpose and use of open loop and closed loop block diagrams.
1.3.5 Differentiate open loop from closed loop process control by identifying negative and positive feedback.
1.3.6 Build examples of open loop and closed loop process control with the aid of block diagrams.
1.3.7 Define automatic control system.
1.3.8 Explain the purpose, advantages and disadvantages of automatic control system usage.
1.4 Identify method of setting up a process control loop system.
1.4.1 Describe the need for a system control diagram.
1.4.2 Explain with the aid of diagrams:
(a) Free single variable loop.
(b) Interacting single variable loop.
(c) Multi -variable loop.
1.4.1 Describe the need for a system control diagram.
1.4.2 Explain with the aid of diagrams:
(a) Free single variable loop.
(b) Interacting single variable loop.
(c) Multi -variable loop.
1.4.3 Identify the need of a cascade control system.
1.4.4 Explain the most important characteristics of a cascade control system with the aid of block diagrams.
1.4.5 Explain the necessity of quality in control system.
1.4.6 Define quality in terms of loop interference,stability, minimal error and minimal duration.
1.4.7 Analyze over-damped, critically damped and under-damped sketching.
1. Open Loop
no feedback
difficult to control output with accuracy
a common example of an open- loop control system is an electric toaster in he kitchen.

2. Close Loop
must have feedback
must have sensor on output
almost always negative feedback
BENEFITS OF OPEN-LOOP SYSTEM
Benefits of an open-loop system are often the small amount of cost associated with running the processes. It is simpler and more cost effective in most cases simply to start a repetitive process without worrying about factoring in feedback. For example, a process of a conveyor belt works more effectively without having to input feedback of the weight of every specific box that it is conveying. In this case, there is no need for feedback to be taken into consideration.
Open Loop System:
Advantages:
Simplicity and stability: they are simpler in their layout and hence are economical and stable too due to their simplicity.
Construction: Since these are having a simple layout so are easier to construct.
Disadvantages:
Accuracy and Reliability: since these systems do not have a feedback mechanism, so they are very inaccurate in terms of result output and hence they are unreliable too.
Due to the absence of a feedback mechanism, they are unable to remove the disturbances occurring from external sources.
EXAMPLE OF OPEN-LOOP SYSTEM?
One example of an open-loop system is a sprinkler system that turns on every day at a pre-programmed time. No matter the moisture level of the grass, the sprinkler system will continue to water it at a prescribed time. (For example, even if there was a heavy rain and the sprinklers do not need to be turned on, they will still water at their pre-programmed time.) That is an open-loop because the sprinklers will turn on no matter the feedback (in this case, the grass moisture). However, if someone were to install a moisture detector where the sprinklers only turn on once it reaches a certain point, then the entire system turns into a closed-loop system.
Open-loop Drying System

FIGURE 1: BLOCK DIAGRAM OF OPEN-LOOP SYSTEM
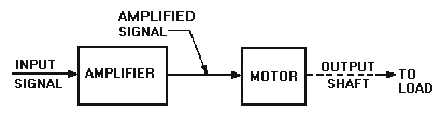
FIGURE 2: OPEN LOOP BLOCK DIAGRAM
CLOSED-LOOP SYSTEM
The opposite of an open-loop system is a closed-loop system. This is a system where the feedback of the process determines the next part of the process. For example, if there is a light that turns on in a room if motion is detected in the room, then that is a closed-loop system since the process of turning on the light entirely depends on feedback, in this case the introduction of motion.
A Closed-loop Control System, also known as a feedback control system is a control system which uses the concept of an open loop system as its forward path but has one or more feedback loops (hence its name) or paths between its output and its input. The reference to "feedback", simply means that some portion of the output is returned "back" to the input to form part of the systems excitation.
Closed-loop systems are designed to automatically achieve and maintain the desired output condition by comparing it with the actual condition. It does this by generating an error signal which is the difference between the output and the reference input. In other words, a "closed-loop system" is a fully automatic control system in which its control action being dependent on the output in some way.
Closed Loop System:
Advantages:
Accuracy: They are more accurate than open loop system due to their complex construction. They are equally accurate and are not disturbed in the presence of non-linearities.
Noise reduction ability: Since they are composed of a feedback mechanism, so they clear out the errors between input and output signals, and hence remain unaffected to the external noise sources.
Disadvantages:
Construction: They are relatively more complex in construction and hence it adds up to the cost making it costlier than open loop system.
Since it consists of feedback loop, it may create oscillatory response of the system and it also reduces the overall gain of the system.
Stability: It is less stable than open loop system but this disadvantage can be striked off since we can make the sensitivity of the system very small so as to make the system as stable as possible.
Closed-loop Control

FIGURE 3: CLOSED LOOP BLOCK DIAGRAM
Method of Setting up A Process Control Loop System
Control System Design
- Establish control goals
- Identify the variables to control
- Write the specifications for the variables
- Establish the system configuration and identify the actuator
- Obtain a model of the process, the actuator and the sensor
- Describe a controller and select key parameters to be adjusted
- Optimize the parameters and analyze the performance
1.4.3 Identify the need of a cascade control system.
The needed of a cascade control system
- A cascade control system is multiple-loop system where the primary variable is controlled by adjusting the set point of a related secondary variable controller. The secondary variable then affects the primary variable through the process.
- Feedback control - Corrective action taken regardless disturbance source.
the set point.
- Problematic for processes with large time constants and/or long
time delays.
- Disturbance must be explicitly measured.- Feed forward control - Corrective action can be taken before the output has deviated from the set point.
Cascade control system contain integrated sets of control loops.
- Primary Loop: Monitors the control variable and uses deviation from its set point to provide an output to the secondary loop.
- Secondary Loop: Receives its set point from the primary loop and controls the reference variable accordingly.
- Effectively accounts for external disturbances
- Reduces dead time in variable response
- Compatible with other control system, such as feed-back and feed-forward control architectures.
- Multiple control loop make physical and computational architecture more complex.
- Additional controllers and sensors can be costly.
No comments:
Post a Comment